Addressing Workforce Challenges in Canada’s Transition to Low-Emission Manufacturing
Disclaimer: The French version of this editorial has been auto-translated and has not been approved by the author.
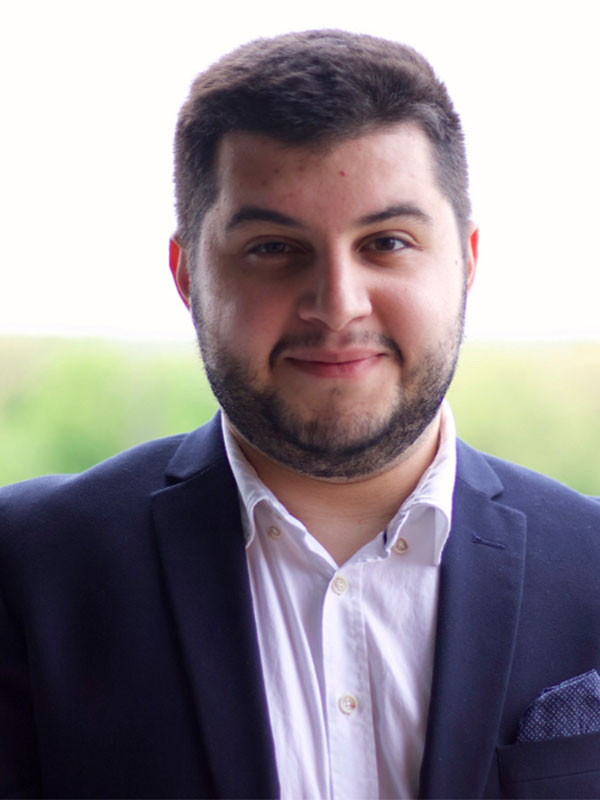
Bassel Kazzaz
Director of Research
Automotive Policy Research Centre & FOCAL Initiative
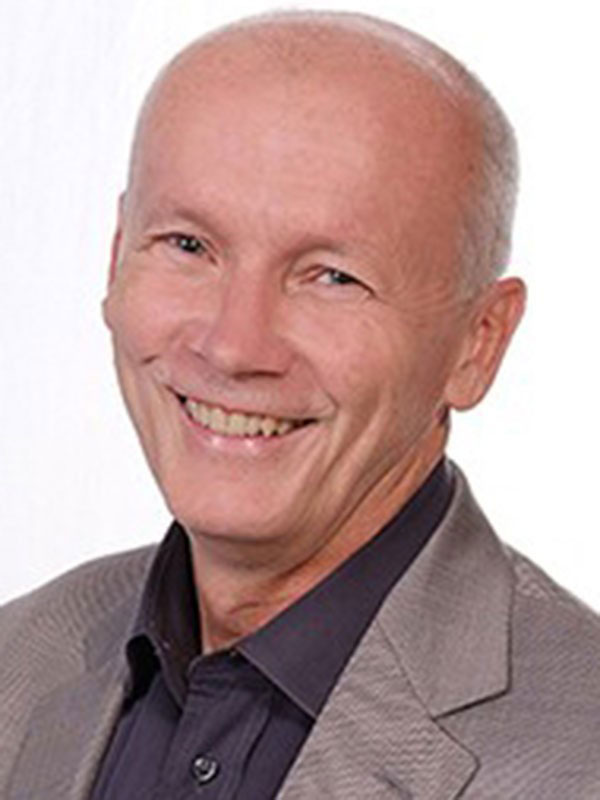
Ken Delaney
Executive Director
Canadian Skills Training and Employment Coalition & FOCAL Initiative
Canada’s manufacturing sector is a key driver of economic growth, innovation, job creation, and trade. In 2023, the sector contributed over C$250 billion to Canada’s GDP, employed over 1.56 million people, and exported over C$450 billion worth of goods. As Canada pushes towards a lower-carbon economy, the sector and its industries are presented with both significant opportunities and challenges. Canada has the opportunity to invest and expand its footprint in manufacturing low or zero-emission technologies, products, and their components, such as electric vehicles (EVs) and their batteries. Canada can also focus on phasing out high carbon footprint processes in manufacturing, and introduce more efficient and low-emission production technologies such as electric arc furnaces (EAF) in steel production. Recent announcements by multiple manufacturers across Canada signal the commitment of companies, governments, and other stakeholders in positioning Canada as a leader in low-emission manufacturing.
However, as Canada’s manufacturing sector transitions to low-carbon products and processes, it faces significant challenges, particularly when it comes to the shortage of skilled labour. Like employers in many other sectors, Canada’s manufacturers will face increasing difficulties in recruiting in the coming years. We have reviewed demographic data and concluded that with increasing retirements and exits of skilled employees in key occupations, and with new job seekers entering those occupations at rates similar to what they have done historically, there will be what we call a recruitment gap. Recruitment gaps are driven by multiple factors, including demand for skilled workers from industry expansion, demand arising from the need to replace retiring employees, and the number of new entrants to the sector. Demographic changes and replacement demand alone has tightened the labour market. With Canada’s big bet on clean technology and sustainable manufacturing, and with the new investment announcements in low-emission technologies and processes, Canada’s demand for skilled labour due to expansion is also expected to rise as more production facilities are established.
Recent research by the Future of Canadian Automotive Labourforce (FOCAL) Initiative demonstrates a growing recruitment gap with the shift to manufacturing low or zero-emission technologies. FOCAL’s research forecasts that with the transition to EV manufacturing in the automotive manufacturing supply chain, the sector will be challenged by a recruitment gap of over 90,000 workers over the upcoming 15 years. Despite some job losses as a result of the anticipated closure of some internal combustion engine manufacturing operations across the Canadian automotive manufacturing supply chain, the expansion in other parts of the EV and battery manufacturing supply chain is expected to not only offset, but also exceed these job losses. FOCAL’s research also demonstrates that all occupational categories, including skilled trades and production occupations, will be key as the automotive manufacturing supply chain transitions to EV and battery production.
Similar challenges are expected in the metal manufacturing industry as it shifts towards low-emission production technologies. With the push to reduce carbon emissions from key industries like steel production, processes such as the implementation of electric arc furnaces (EAF) and hydrogen-based steelmaking are becoming more prevalent. While these advancements reduce carbon emissions significantly during production, the implementation, operation and maintenance of these technologies require skilled labour. The metal manufacturing industry, much like automotive manufacturing, is expected to face challenges in recruiting skilled workers.
According to recent data by Statistics Canada, over 47 per cent of manufacturing companies have been facing recruitment challenges, particularly when it comes to hiring skilled workers. The manufacturing workforce is growing older, with more than a quarter of workers now aged 55 or older. Without the supply of skilled trades, the sector is likely to face productivity slowdowns and the inability to meet the increasing demand for low-carbon products and technologies. This growing challenge is exacerbated by the fact that many younger workers are not entering the manufacturing sector at a rate sufficient to replace retirees. As a result, there is a need for focused efforts on talent recruitment and reskilling initiatives to attract and train a new generation of workers in advanced manufacturing technologies.
Despite the introduction of advanced technologies in multiple industries within manufacturing, the role of many traditional occupations remains critical within the sector. Canada’s ability to seize the opportunities presented by its investments in clean technology and sustainable manufacturing will depend on addressing the shortage of skilled labour. Yes, we need scientists, designers, and engineers with advanced capabilities. But we also need forklift operators, miners, millwrights, electricians, and tool and die makers. The implementation of training programs tailored to the evolving needs of the manufacturing sector, such as apprenticeships and specialized education in green technologies, is critical. Without a sufficient pool of trained workers, the sector risks stalling in its efforts to adopt innovative, low-emission technologies.